Welcome to Deviation Investigations and Investigation Report Writing, an advanced CGMP training course.
Deviation Investigations
The CGMP Require in Sec. 211.100 (b) Written procedures; deviations. (b) Any deviation from the written procedures shall be recorded and justified.
Learn to use the most effective tools to investigate a plant, laboratory or customer service deviation.
Presentations cover the following topics:
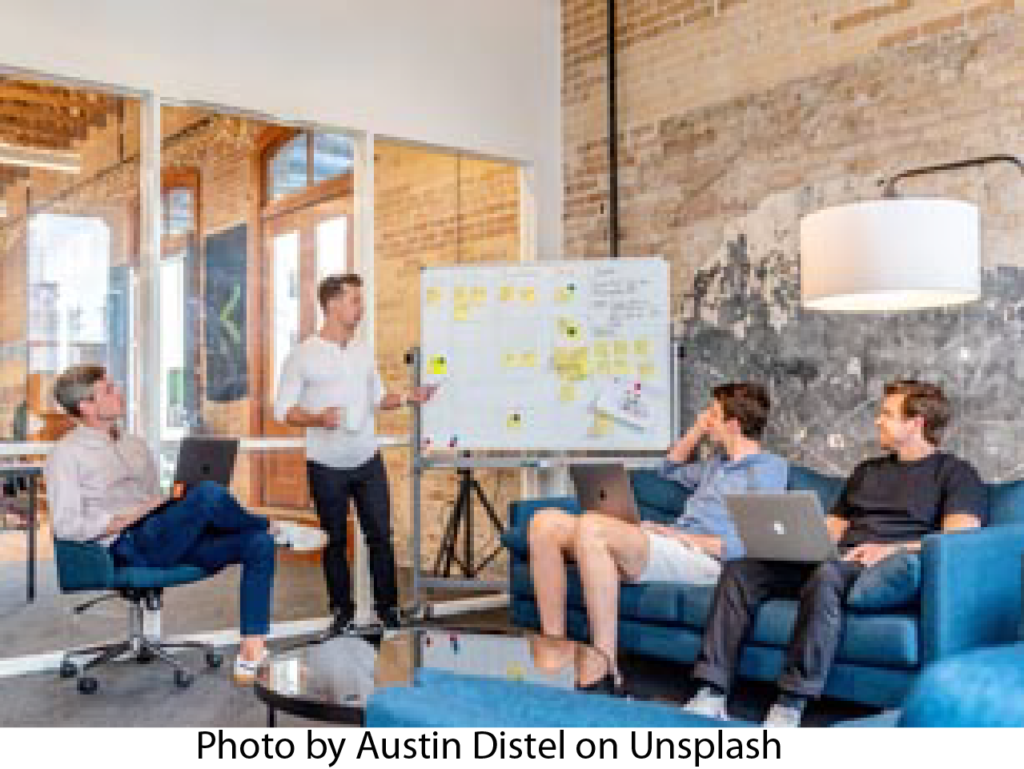
- Introduction to Root Cause Analysis
- Deviation Investigation Terms
- Interviewing and Path Forward
- Root Cause Analysis: Fish Bone Diagrams
- Five Why’s Mapping
- Distinctions
- Walk-Through-Analysis
- Change Analysis
- Understanding Human Errors
- Control Barrier Analysis
- Determine Product Impact
- Research Previous Investigations
- Immediate Actions and Containment
- Corrections
- Corrective Actions
- Preventive Actions
- Follow up and CAPA Effectiveness Checks
- Risk Assessment
Email us or give us a call to discuss your training needs. Simply contact us!
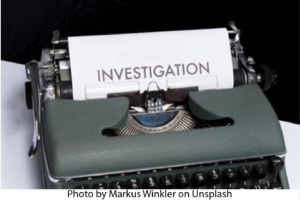
Deviation Investigation Report Writing
Learn to write deviation investigation reports that meet the needs of the company, quality assurance and the FDA.
Presentations cover the following topics:
- Introduction to Deviation Report Writing
- Writing Tips
- Description of the Event
- Event Classification
- Immediate Actions and Containment
- Previous Investigation Summaries
- The Sequence of Events
- Root Cause Summary
- Product Impact
- Corrective and Preventive Actions
- Report Follow UP Actions and Effectiveness Checks
- The Proper Use of Background Information
- Using Attachments
- Referential Information
- Interim Reports and Deviation Extensions
Email us or give us a call to discuss your training needs. Simply contact us!
One-on-one personal coaching is provided on the use of each tool or section of the deviation investigation report. Coaching builds and reinforces skills.
How this course works on-line
- Employees view a presentation authored and presented by a seasoned deviation investigator.
- Employees complete the associated worksheet apply to an actual in-your-plant deviation the tool or report section just discussed. (non disclosures will be signed ahead of enrollment).
- A seasoned investigator will review the employee’s work and email to the employees specific comments addressing what work is a good representation of the tool and other areas to consider in the investigation process, including clarification of CGMP regulations impacting the deviation being investigated.
- When the instructor has passed the employee on a particular tool, then the employee is encouraged to move on to the next topic.
- Online internet-based e-learning, is designed to fit your schedule, 365 x 24 x 7. Come and go as needed. What is e-learning? Therefore, our courses are convenient and flexible.
- Above all, if you have questions, please e-mail us for the fastest response at jennifer.payne@skillsplusinc.com
Optional course for more in depth CGMP Understanding
- If you need more in depth CGMP understanding, we encourage the employee to sign up for The New Generation Series.